In the realm of fluid management, the choice between a ball valve and a gate valve can make or break system efficiency.
Ball valves offer rapid 90-degree on/off action, perfect for quick shut-offs, while gate valves minimize flow resistance when fully open, ideal for large pipelines.
One excels in tight sealing, the other in handling high pressures.
Curious which one is the better fit for your project?
Uncover the detailed differences and find your perfect valve match.
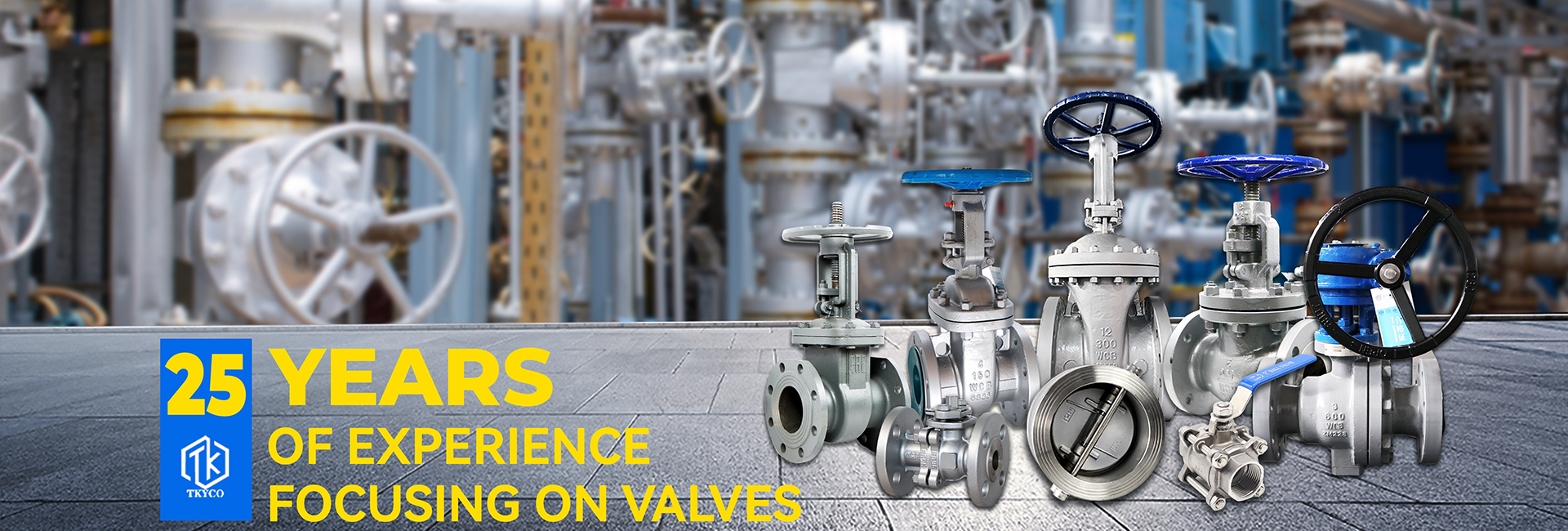
Why Valve Selection Matters?
Valve selection is critically important in any system that handles fluids (liquids, gases, slurries) because the wrong valve can lead to a cascade of problems, impacting safety, efficiency, and cost. Here's a breakdown of why it matters:
1. Safety:
-Preventing Catastrophic Failures: Incorrectly chosen valves can fail under pressure, temperature, or chemical attack, leading to leaks, bursts, fires, or explosions, especially with hazardous materials. Relief valves, for instance, are essential safety devices that prevent overpressure.
-Protecting Personnel: Leaks or uncontrolled releases can expose workers to dangerous substances, causing injuries or health problems.
-Maintaining System Integrity: The right valve prevents damage to other system components by controlling flow and pressure within safe limits.
2. Optimal Performance and Efficiency:
-Precise Control: Different applications require different levels of flow control (on/off, throttling, mixing, diverting). Selecting the right valve type (e.g., ball valve for on/off, globe valve for throttling, check valve for one-directional flow) ensures the system operates as intended.
-Proper Flow Rate: Oversized valves can lead to poor control and instability, while undersized valves restrict flow, cause excessive pressure drops, and increase energy consumption. The flow coefficient (Cv) is a crucial factor here.
-Reduced Energy Consumption: An efficiently operating valve minimizes pressure losses and turbulence, leading to lower energy requirements for pumps and compressors.
-Consistent Production: Accurate flow and pressure control contribute to stable and consistent production results, leading to higher quality products.
3. Cost Savings:
-Reduced Maintenance and Downtime: A properly selected valve is more durable and requires less frequent maintenance, minimizing costly shutdowns and repairs.
-Extended Equipment Life: When a valve is matched to its application, it experiences less wear and tear, extending its own lifespan and potentially the lifespan of other connected equipment.
-Lower Operating Costs: Efficient operation translates directly to lower energy bills and reduced material waste.
4. Longevity and Reliability:
-Material Compatibility: The valve's materials (body, trim, seals) must be compatible with the media it handles, as well as the ambient environment. Incompatible materials can lead to corrosion, erosion, embrittlement, or stress cracking.
-Temperature and Pressure Ratings: Valves must be rated to withstand the maximum and minimum temperatures and pressures of the process fluid and the operating environment.
-Wear Resistance: For abrasive or erosive fluids, materials with high wear resistance are crucial to prevent premature degradation.
-Cycle Life: For applications requiring frequent operation, a valve designed for high cycle life is essential.
5. Compliance and Environmental Impact:
-Meeting Industry Standards: Many industries have strict regulations and standards for valve selection and performance. Proper selection ensures compliance and avoids penalties.
-Environmental Protection: Preventing leaks and uncontrolled releases of fluids (especially hazardous ones) is vital for protecting the environment.
What is Ball Valve?
A ball valve is a quarter-turn valve that uses a hollow, perforated sphere to control flow. When the hole aligns with the pipeline, fluid passes through freely; when turned 90 degrees, flow is blocked. Known for quick shut-off, tight sealing, and corrosion resistance, ball valves are widely used in industries like oil and gas, water treatment, and chemical processing due to their reliability and minimal leakage.
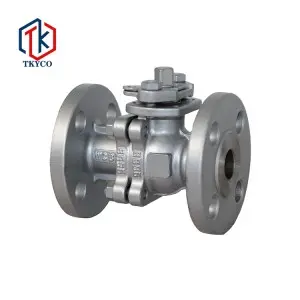
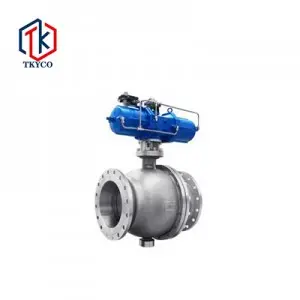
What is Gate Valve?
A gate valve is a shut-off valve that controls fluid flow by lifting or lowering a gate inside the valve body. When open, it provides a straight, unobstructed path with minimal pressure drop. It operates slowly via linear motion, making it ideal for full-flow applications—not throttling. Gate valves are widely used in water systems, oil refineries, and steam lines due to their reliable sealing and ability to handle high pressure and temperature.
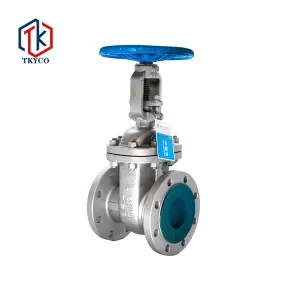
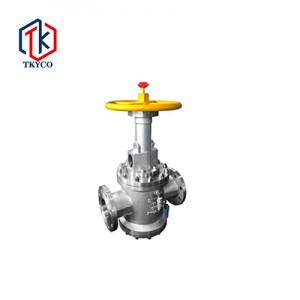
Key Differences Between Ball Valve and Gate Valve
1. Operation and Flow Control
A ball valve operates by rotating a ball with a hole through it by 90 degrees, allowing or stopping flow instantly. This quick action makes it ideal for fast shut-off but may cause water hammer in sensitive systems. It is not suitable for throttling because partial opening can erode the seats and cause leaks.
In contrast, a gate valve uses a gate that moves up and down to control flow. It requires multiple turns to operate, which helps reduce the risk of water hammer. Although it can throttle flow, doing so can damage the gate and reduce sealing efficiency.
2. Sealing and Leakage
Ball valves offer a very tight seal due to their design, even after long periods of disuse. They are less likely to leak because they have fewer potential leak paths and use soft seats pressed firmly against the ball.
Gate valves provide adequate sealing when fully closed, but their sealing surfaces can wear with frequent use, increasing the risk of leakage. They are also more prone to leaks around the stem due to the linear movement during operation.
3. Pressure Drop and Flow Characteristics
When open, ball valves allow flow through a nearly straight path, resulting in minimal pressure drop. Full-port designs match the pipe diameter for optimal flow, while reduced-port versions are more compact but may slightly reduce flow.
Gate valves also offer a straight, unobstructed flow path when fully open, making them excellent for high-flow applications with very low pressure loss.
4. Durability and Maintenance
Ball valves tend to be more durable and low-maintenance, thanks to fewer moving parts and a rotary motion that minimizes stem wear. Their simple mechanism also makes them easy to automate.
Gate valves are more prone to wear over time, especially if not used correctly or exposed to abrasive fluids. They often require more maintenance, particularly around the stem packing.
Advantages of Ball Valve and Gate Valve
Advantages of Ball Valve
1. Quick Operation: Ball valves feature a quarter-turn mechanism, allowing for rapid opening and closing. This makes them ideal for applications that require immediate shut-off, such as emergency response systems or automated processes.
2. Tight Sealing: Their spherical design ensures an excellent seal when closed, minimizing the risk of leakage. This is crucial for handling hazardous or costly fluids, making ball valves a top choice in the chemical and petrochemical industries.
3. Low Maintenance: With fewer moving parts compared to some other valves, ball valves tend to have longer lifespans and require less frequent servicing. Their simple structure reduces wear and tear, cutting down on maintenance costs over time.
4. Versatile Applications: Suitable for various media, including liquids, gases, and slurries, ball valves can operate across a wide range of temperatures and pressures. Their adaptability makes them popular in sectors like water treatment, oil and gas, and food processing.
5. Precise Flow Control: While primarily used for on/off functions, certain ball valves with V - shaped or port - sized bores can provide effective throttling capabilities, enabling more nuanced flow regulation.
Advantages of Gate Valve
1. Minimal Flow Resistance: When fully open, gate valves offer a straight - through flow path with minimal turbulence and pressure drop. This unobstructed flow makes them highly efficient for large - scale pipelines in industries like water supply, oil and gas transmission, where maintaining flow velocity is crucial.
3. High - Pressure and High - Temperature Tolerance: Constructed with robust materials such as cast iron, stainless steel, or forged steel, gate valves can withstand extreme pressures and temperatures. This makes them suitable for demanding environments like power plants, refineries, and industrial steam systems.
5. Cost - Effective for Large - Diameter Pipelines: For large - bore pipelines, gate valves are often more economical than alternatives. Their straightforward structure and ease of manufacturing contribute to lower production costs, making them a practical choice for projects where budget and performance need to be balanced.
Considerations for Choosing the Right Valves: Ball Valve or Gate Valve?
When comparing ball valves and gate valves, their core performance differences lie in operation, sealing, and flow characteristics.
① Prioritize Ball Valves When:
- Quick Operation is Essential: In emergency shut - off systems or automated processes that require immediate flow interruption.
- Leak - Tight Sealing Matters: When handling hazardous, expensive, or corrosive fluids, such as in chemical plants or pharmaceutical manufacturing.
- Moderate Throttling is Needed: For applications where some degree of flow adjustment is required, like regulating water flow in small - scale irrigation systems.
② Opt for Gate Valves When:
- Unobstructed Flow is Critical: In large - diameter pipelines for water distribution, oil and gas transmission, where minimizing pressure drop is key.
- Long - Term Shut - Off is Required: For isolating sections of pipelines during maintenance or in systems that operate mostly in fully open or closed states, like in power plants.
Special Scenarios:
- High - Temperature and High - Pressure Environments: Gate valves are often preferred due to their robust construction and ability to withstand extreme conditions, but high - performance ball valves with specialized materials can also be suitable if quick operation and tight sealing are needed simultaneously.
- Slurry or Viscous Media: Ball valves with a full - port design can handle slurries well, preventing blockages, while gate valves may struggle if the media causes the gate to stick or accumulate debris.
In summary, the choice between ball valves and gate valves depends on your specific needs.
Ball valves are best for quick on/off control and tight sealing, making them suitable for handling hazardous fluids and emergency shut-offs.
Gate valves excel in providing unobstructed flow and handling high pressure, ideal for large pipelines and long-term shut-off applications.
Consider your fluid type, operating conditions, and specific requirements to make the right choice for your system.
Post time: Jun-23-2025